Quote from: giovanotti on January 25, 2014, 11:40:43 AMLet me revive this topic.
Team work. Comments welcome.
As said long time ago, I am using Thien baffle between 5 gallon bucket and shopvac's bucket. Small Thien on left not used.
My problem is ultrafine dust as it cloggs vac's textile filters. Have to clean them on weekly basis - annoying.
Idea in works: install another baffle within shopvac's bucket. This time Thien buffles would have approx 70mm (2,7 in) in diameter, there would be 5 of them. For the beginning made of CNC cut styrofoam.
Idea:
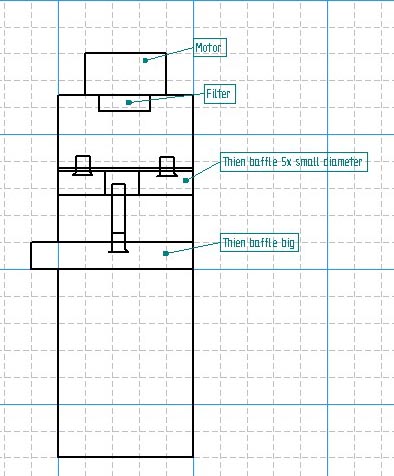